Wenn man sich in der Konzernzentrale bei Norsk Hydro in Oslo Ziele setzt, dann hat das ernsthafte Konsequenzen für die rund 35.000 Mitarbeiter in 40 Ländern auf allen Kontinenten dieser Erde. Die Vorgabe: Nachhaltigkeit.
FOTOS: TM-HECHENBERGER, MATTHIAS RHOMBERG
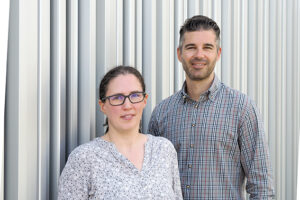
Bei der Arbeitssicherheit zum Beispiel, deren Optimierung man sich schon in den 1980er-Jahren vorgenommen hat, sind die „Wikinger” längst international führend. Ihre generellen Strategien und bis ins kleinste Detail ausgearbeiteten Maßnahmen zur Vermeidung von Unfällen sind heute Vorbild für tausende Produktionsbetriebe weltweit. Seit einiger Zeit ist Nachhaltigkeit das große Thema bei Hydro. Eine Messgröße dafür ist der „CO2-Fußabdruck”. Sämtliche Kohlendioxid-Emissionen, die von der Gewinnung des Rohstoffs Bauxit bis zum Recycling der Aluminiumprodukte anfallen, werden dafür addiert. Je kleiner der Fußabdruck des Unternehmens, desto besser.
Bei Hydro in Nenzing hat Geschäftsführer Manfred Rotschne das Ziel ausgegeben, den CO2-Fußabdruck gegenüber dem Referenzjahr 2018 bis 2030 um 30 Prozent zu reduzieren. Florian Schnetzer und Sandra Brändle kümmern sich „hauptamtlich” um diesen Themenkomplex. Und der ist ziemlich umfangreich, wie die beiden überzeugend darlegen.„Aluminium ist nicht gleich Aluminium”, stellt Florian Schnetzer klar. Bei der Produktion von einem Kilo Aluminium werden im weltweiten Durchschnitt rund 16,7 Kilogramm CO2 freigesetzt.
Das Aluminium der Norsk-Hydro-Gruppe verursacht demgegenüber im Durchschnitt nur etwa 5,7 Kilo CO2-Emissionen. Außerdem bietet Hydro ihren Kunden die Aluminiumsorten „Reduxa” (Aluminium mit nur 4,0 Kilo CO2-Emissionen) und „Circal” (aus 75 Prozent Recyclingaluminium mit gerade noch 2,3 Kilo Emissionen). Für diese zertifizierten Spezialsorten rührt Hydro Nenzing bei ihren Kunden – das sind über tausend (!) Großabnehmer in Süddeutschland, der Schweiz und Österreich – die Werbetrommel kräftig. Nachhaltigere Materialien, die mit geringeren Emissionen produziert werden, werden schließlich zu nachhaltigeren Kunden-Produkten beitragen. Die Kunden, die mit den Nenzinger Aluprofilen etwa Fassadenelemente, Türstöcke oder Fenster herstellen, profitieren. „Die Verwendung von nachhaltigeren Baustoffen wie Reduxa oder Circal und der Nachweis eines ökologischen Fußabdruckes auf Produktebene ist gerade bei öffentlichen Auftragsvergaben schon heute ein Wettbewerbsvorteil”, betont Sandra Brändle. Sie registriert darüber hinaus, dass auch immer mehr Privatpersonen bereit sind, für diese nachhaltigeren Produkte einen Aufpreis zu bezahlen.
Wettbewerbsvorteil durch Umweltschutz
Dieser Trend ist für die Ziele bei Hydro Nenzing natürlich günstig. „Um ganzheitliche Optimierungen zu erreichen, müssen wir aber wirklich an allen Rädchen drehen: Energieeinsatz, Material- und Hilfsstoffeinsatz, Abfallaufkommen, Design und vieles mehr”, so Florian Schnetzer. Sämtliche Stapler fahren zum Beispiel schon lange mit Strom statt Diesel. Auch die Beleuchtung wurde bereits fast vollständig von Halogenlampen auf energiesparende LED umgestellt. Deutlich am meisten Energie wird im Werk Nenzing für das Pressen der Aluprofile aufgewendet. Um hier möglichst viel einzusparen, wurden Millionen für den Austausch bzw. die Erneuerung von Pressen, Hydraulik oder Motoren für Kühlung und Antrieb investiert. „Zur Nachhaltigkeit gehört ja auch, dass man bestehende Systeme so lange wie möglich und sinnvoll nutzt”, erläutert Schnetzer.
Für die Verarbeitung des Aluminiums ist sehr viel Wärmeenergie erforderlich. Das Alu selbst wird auf circa 500 Grad erwärmt und auch die erforderlichen Werkzeuge (je nach Profilform zwischen 20 und 100 Kilo schwere Matrizen) müssen eine ähnliche Temperatur haben, bevor das Metall mit großem Druck durch die Werkzeuge gepresst werden kann. Sie werden dafür in einem Ofen vorgeheizt. Durch die Analyse der Aufheizzeiten konnte die Verweildauer im Ofen und die Belegung optimiert werden, sodass nicht mehr Öfen als notwendig im Betrieb sind: dadurch können viele Kilowattstunden Strom eingespart werden, was sich positiv auf den Fußabdruck auswirkt.
Alle Prozesse werden durchleuchtet
Der Nachhaltigkeit wegen wurde auch beim Fräsen und Bohren der Aluminiumwerkstücke das System umgestellt: Herkömmliche Bohrer und Fräser müssen je nach Anwendung mit sogenanntem Schneidöl oder mit Kühlschmiermittel gekühlt werden. Dieses Öl verschmutzt sowohl die Produkte als auch die Aluminiumspäne, welche dadurch nur mehr mit großem Aufwand dem Recycling zugeführt werden können. Mit der (ziemlich teuren) Anschaffung von speziellen Werkzeugen mit einer besonderen Schnittgeometrie sowie einer innovativen Beschichtung kann auf das Öl verzichtet werden. Das hat auch eine positive Auswirkung auf die Umgebungsluft und damit auf die Mitarbeiter, weil keine problematischen Aerosole mehr freigesetzt werden.
Die im Lauf der Jahre in Nenzing durchgeführten Optimierungen haben dazu beigetragen, dass der spezifische Energieverbrauch pro Tonne gepresstes Aluminium auf mittlerweile unter 800 kWh reduziert werden konnte. Der durchschnittliche spezifische Energieverbrauch der europäischen Hydrowerke ist mit 1.100 kWH pro Tonne bedeutend höher. Um das Gesamtziel zu erreichen, werden in den kommenden Jahren noch viele weitere Maßnahmen folgen.
________________________________________________________________________
Aluminium ist das häufigste Metall in der Erdkruste. Entdeckt wurde es aber erst Mitte des 18. Jahrhunderts: Weil es kaum in reiner Form, sondern hauptsächlich in verschiedensten chemischen Verbindungen vorkommt. Erst 1889 wurde das nach seinem Schöpfer – dem steirischen Chemiker Carl Joseph Bayer – benannte und heute noch angewandte „Bayer-Verfahren” erfunden, das die industrielle Produktion von Aluminium aus Bauxit-Gestein ermöglicht. Damit begann der Siegeszug des äußerst vielseitigen Metalls, das federleicht und – mit anderen Elementen gemischt – hart wie Stahl ist, das hitzefest, extrem verformbar und korrosionsbeständig ist. Aluminium ist nach Stahl der zweitwichtigste metallische Werkstoff. Im Vorjahr wurden weltweit rund 63 Millionen Tonnen davon produziert. Die globale Recycling-Quote beträgt (laut Wikipedia) derzeit 40 Prozent. Technisch wären annähernd 100 Prozent möglich.