In zwei gigantischen Öfen werden in Schlins jährlich bis zu 90.000 Tonnen Aluminiumschrott erhitzt. Bei Temperaturen von rund 700 Grad Celsius schmilzt das Material und wird in hochpräzisen Verfahren für die Wiederverwendung in Bolzen gegossen. Die „Speedline Aluminium” Recycling-Bolzen sind gefragt. Ein dritter Ofen ist in Planung.
FOTOS: TM-HECHENBERGER
„Was wir täglich machen, ist direkter Umweltschutz”, erklärt DI Alexander Plakolm. Der gebürtige Bludenzer, der an den Technischen Universitäten in Wien und Graz studierte, ist seit einem Jahr mit hauptverantwortlich für den reibungslosen Ablauf bei „Speedline Aluminium”.
„Das Thema Sicherheit steht dabei immer absolut im Vordergrund”, betont Plakolm – und beim Rundgang durch den Betrieb (natürlich nach vorheriger halbstündiger Anweisung und in voller Schutzbekleidung) wird augenscheinlich, dass das durchaus seine Berechtigung hat.
Auf dem Lagerplatz bewegen riesige Radlader die täglich von rund zwanzig Lastwagen angelieferten Schrottmengen und die von den meist gleichen Lastwagen von den Kunden georderten Strangpressbolzen – die bis zu acht Meter lang und 1,3 Tonnen schwer sind. Täglich fünf bis sechs Mal wird der Schmelzofen mit jeweils gut 50 Tonnen neuem Schrott befüllt. Dieser Aluschrott stammt von Händlern und Kunden der aluverarbeitenden Industrie und wird bei der Anlieferung mittels Lichtbogen-Analyse genau auf seine chemische Zusammensetzung überprüft.
Aluminium ist ein äußerst vielseitiges Material: Leichte Kochtöpfe, verwindungssteife Fensterrahmen oder „unkaputtbare” Fassadenelemente können damit hergestellt werden. In der Fahrzeugindustrie und in der Raumfahrt bewährt sich Aluminium ebenfalls. Seine spezifischen Eigenschaften kann man durch die Beimengung von Silicium, Magnesium, Mangan, Kupfer, Zink und anderen Stoffen sehr genau steuern.
Wenn die jeweils 52 Tonnen Aluschrott nach etwa vier Stunden Gasbefeuerung im Schmelzofen flüssig geworden sind, wird die Schmelze in den Gießofen geleitet. Ein riesiges elektromagnetisches Rührwerk sorgt unter dem Ofen für eine gleichmäßige Verteilung der Inhaltsstoffe. Und die müssen genau der vom Kunden gewünschten Legierung entsprechen.
Dabei geht es beispielsweise darum, dass im heißen Brei maximal 0,03 Prozent Zink enthalten sein dürfen. Höchstens 15 Kilo auf 50 Tonnen also. Liegt der Wert unter dem Minimum, werden ein paar Gramm Zink zugemischt – kein Problem. Liegt der Wert aber über dem Maximum, kann der zu hohe Anteil nur durch die Zugabe von Primäraluminium (fast reines Aluminium) gesenkt werden. Das ist aber nur begrenzt möglich, weil der Ofen ja fast ganz gefüllt ist. „Deswegen ist es wichtig, dass wir den gelieferten Schrott genau analysieren und die Sorten für die jeweils geforderte Legierung entsprechend zusammenstellen”, erklärt Alexander Plakolm.
Möglichst wenig Reinaluminium zu verwenden, ist auch aus einem anderen Grund wichtig. Für dessen Herstellung aus Bauxit wird viel Energie benötigt. Je nach der verwendeten Energiequelle schleppt jede Tonne Primäraluminium einen „Rucksack” von rund vier Tonnen (Wasserkraft) bis 18 Tonnen (Kohle) CO2 mit sich. Bei wiederverwertetem Alu verbessert sich die Umweltbilanz deutlich – speziell, wenn bei dessen Herstellung wenig Reinaluminium verwendet wird.
Das Speedline-Aluminium weist einen durch ein „EPD-Zertifikat” bestätigten Spitzenwert von nur 1,9 Tonnen CO2 aus. Das erreicht man unter anderem dadurch, dass für die neuen Bolzen jedes Kunden möglichst viel von dessen eigenem und separat aufbewahrtem Schrott, der ja die richtige Legierung aufweist, verwendet wird. „Das Know-how und die Sorgfalt unserer Mitarbeiter sowie modernste Technik machen das möglich”, ist der Bereichsleiter stolz auf seine Crew, die aus derzeit insgesamt 50 Mitarbeitern besteht.
Müssen die Öfen – zum Beispiel für die jährliche Revision – abgeschaltet werden, dauert es 15 Tage, bis sie entsprechend abgekühlt und wieder auf Betriebstemperatur aufgeheizt sind. „Die Anlage an jedem Wochenende abzustellen – das geht sich also nicht aus”, erläutert Plakolm. Für die Mitarbeiter in der Produktion heißt das, dass ganzjährig im Vier-Schicht-Betrieb gearbeitet werden muss.
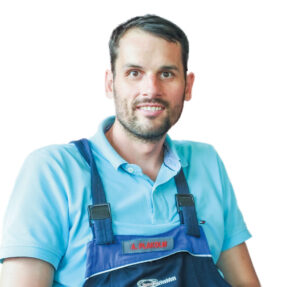
„Dafür werden die Speedliner aber weit über dem Durchschnitt entlohnt”, wirft Plakolm ein gewichtiges Argument in die Waagschale. Letztlich, davon ist Plakolm überzeugt, gehe es bei der Wahl der Arbeitsstelle aber auch um ein gutes Betriebsklima und darum, gemeinsam mit motivierten Kollegen etwas Sinnvolles zu tun. Und schließlich ist die 1980 vom allzu früh verstorbenen visionären Nüziger Unternehmer Günter Steinacher gegründete „Alu-Met” in Bludenz ein verlässlicher und finanzstarker Arbeitgeber. Zur Alu-Met, die seit 2021 vom international erfolgreichen Topmanager Dr. Gerhard Anger geführt wird, gehört neben Speedline in Schlins auch die Aluminium GmbH Nachrodt (AGN) in Deutschland.
So gesehen ist Alexander Plakolm zuversichtlich, in den nächsten Wochen und Monaten bald neue Mitarbeiterinnen und Mitarbeiter begrüßen zu dürfen. Es steht nämlich eine Millioneninvestition für einen weiteren „heißen Ofen” an, mit dem das Primäraluminium „vorgewärmt” wird, bevor dieses in den Schmelzofen kommt. So kann die jährliche Produktion von derzeit 80.000 Tonnen auf die bewilligten 96.000 Tonnen gesteigert werden. Vor allem aber wird sich dadurch der Gesamtenergieverbrauch je Tonne verringern.
„Das steigende Umweltbewusstsein spricht an sich schon für den praktisch unendlich recycelbaren Werkstoff Aluminium. Und wenn wir unsere Recyclingtechnik weiter perfektionieren, wird das die Nachfrage noch einmal befeuern”, ist Plakolm überzeugt.